Drywall is an essential construction material, but improper installation can lead to problems that require costly repair. To ensure a successful project, builders must balance cost with quality and precision.
Measuring framing spacing to determine the right drywall size makes for accurate cuts. A well-planned layout minimizes waste and reduces the number of seams. Click the Drywall Installation Naperville to learn more.
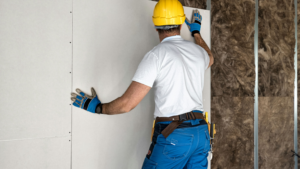
Whether you’re installing drywall in your home or doing a commercial project, proper preparation is key to a successful outcome. By assessing the space, gathering necessary tools and materials, installing blocking and electrical outlets, and protecting floors and surfaces, you can streamline the installation process and achieve professional results.
Start by measuring the space you need to cover and determining how much drywall you’ll need. Make sure you have a few extra sheets on hand for waste and cutting mistakes, and plan ahead by marking where any studs or electrical outlets will be located.
You should also decide whether you will hang the drywall horizontally or vertically. Horizontal installation helps prevent warping and bending and reduces the number of seams, while vertical installation is ideal for tall walls or when working alone. It’s also a good idea to stagger the seams where possible, as this will help reinforce the wall and conceal them later on.
Before you begin putting up the drywall, be sure to lay down tarps or drop cloths to protect your floors and furnishings from dust and debris. This will also help to make cleanup easier. It’s also a good idea for workers to wear masks, as drywall dust can irritate the nose and throat when inhaled.
The next step is to prep the drywall surface by smoothing and sanding it. Then, apply a primer to help seal the porous surface and prevent the formation of mold or other harmful substances. Finally, apply a high-quality drywall paint to provide a long-lasting finish.
Installing Blocking
If you’re hanging heavy objects, like cabinets or shelves, on your drywall, you should install blocking before beginning the installation process. This will add additional support to the drywall, helping it to resist warping and bending and ensuring that your fixtures are secure.
Before installing a corner bead, you should make sure it’s fastened securely to the drywall and firmly attached to the framing members. Once the bead is in place, you can apply a liberal amount of joint compound over it. Be sure to apply the compound evenly so that it looks consistent and free of blemishes.
Hanging
Drywall is an ideal building material for home renovations and additions. It can be a DIY project, but the job requires time and effort to install properly. It’s best to hire a professional who can ensure that the project is completed correctly and on budget. Drywall installation costs include materials, labor, and other related expenses. It’s important to take the time to plan out the job and understand all of the steps involved.
First, measure and mark your drywall sheet to determine how much you need to cut. This will save you time when cutting, and it helps prevent mistakes. Then, lay the sheet on a flat surface and use a drywall saw to cut it along the marks. After the drywall is cut, you can begin installing it on the wall.
When hanging drywall, you should always screw each piece of wallboard to the framing using appropriate screws. Make sure that the heads of the screws are not recessed in the face paper and that they’re countersunk below the surface of the wallboard. This will help prevent cracks from forming as the wallboard expands and contracts.
Next, you need to cut out any necessary openings for doors, windows, and electrical outlets. You can use a drywall saw or a circular saw with a drywall blade. For large openings, you may need to use a drywall router.
Hanging drywall can be difficult, especially when working alone. It’s recommended that you have someone assist you with the process, as drywall sheets are heavy to lift. It’s also a good idea to label each panel with points of reference to help you identify the correct side to hang.
It’s also a good idea to stagger the seams in your wallboard. This will add strength to your walls and minimize the amount of patching required. It will also help make it easier to conceal any imperfections in your wallboard with paint and trim. You can use a tape measure to determine the distance between each joint. If you’re working on a commercial project, fire codes will require that all of the seams be vertical. For residential jobs, however, you can choose to hang the drywall horizontally instead.
Taping
Drywall installation is a process that requires attention to detail for a quality result. While hanging drywall is relatively straightforward, the finishing phases of mudding and taping take more skill and precision to get right. For this reason, a DIY homeowner might want to leave this step to a professional drywall specialist for the best results.
The type of tape used to seam drywall is important, and there are several different options available. The primary two choices are paper and mesh tape. Both have unique characteristics that make them better suited for different scenarios.
Paper drywall tape is inexpensive and easy to work with, making it ideal for standard seams. It is also a good choice for corners because it can be folded easily into and over them. It is non-adhesive, however, and must be embedded in a layer of joint compound before it will stick. It is also susceptible to wrinkling or bubbling if not applied carefully and with proper technique. Paper tape is not suitable for use in high-moisture areas as it can become weak when exposed to water.
Mesh drywall tape is composed of fiberglass threads that are both stronger and more durable than paper tape. It is resistant to mold, making it a better option for bathrooms or kitchens. It is also easier to work with than paper tape, and it has an open mesh structure that allows joint compound to penetrate and bond effectively. It can be purchased at most hardware stores and is a popular choice for professionals.
Regardless of the type of tape used, there are certain things all professionals should do to ensure that the finished product is top-notch. First and foremost, all professionals should adhere to safety protocols and wear personal protective equipment (PPE) throughout the project. This will ensure their own safety as well as the safety of others working on site.
Professionals should also keep a clean and organized work area, keeping tools, materials, and debris in a designated place at all times. This will minimize the risk of accidents and help to maintain a high level of professionalism.
Finishing
After you’ve taped and sanded your interior walls, the next step is to finish them so they’re ready for painting or wallpapering. Having the right tools for this can help you create a professional-looking wall. You’ll need putty knives, preferably in two sizes: a small one for getting into corners and a wider one for feathering out the compound. You’ll also need joint compound or mud, available premixed or in a bucket. It’s important to select the right type of mud for your project, as some can be used for ceilings while others are not.
The first step in finishing is to apply a skim coat. This is a very light layer of mud that’s designed to smooth out the surface for painting. It’s a good idea to mix water into the mud for easier application. You don’t want the mud to be too runny though, as this could expose the tape and lead to visible seams.
Once the mud has dried, you can apply more layers of mud as needed, always using a light touch to avoid exposing the tape. You’ll need to sand between coats, too, so make sure you’re using a fine-grit sandpaper.
When you’re ready to cut a piece of drywall, use a T-square and utility knife to score the front side of the sheet, at least 1/8” deep (Image 2). Then, push down on the backside with your knee, snapping it along the scored line. Be careful not to rip the paper backing.
Inside corners require a different technique, as they’re harder to reach with a blade. To create a clean, sharp corner, you can use a tool called a Trim-Tex Magic interior corner. This is much easier to use than taping and sanding, and it’ll give your walls a polished look.
While completing a drywall project on your own may seem daunting, it is possible to do if you follow the steps carefully and take your time. The rewards will be worth the effort, resulting in a finished wall that’s ready for painting or other decoration.